સેમિકન્ડક્ટર ઉત્પાદન પ્રક્રિયામાં એક મહત્વપૂર્ણ પગલું તરીકે, વેફર ડાયસિંગ ટેકનોલોજી, ચિપ કામગીરી, ઉપજ અને ઉત્પાદન ખર્ચ સાથે સીધી રીતે જોડાયેલી છે.
#01 વેફર ડાઇસિંગની પૃષ્ઠભૂમિ અને મહત્વ
૧.૧ વેફર ડાઇસિંગની વ્યાખ્યા
વેફર ડાયસિંગ (જેને સ્ક્રિબિંગ તરીકે પણ ઓળખવામાં આવે છે) એ સેમિકન્ડક્ટર ઉત્પાદનમાં એક આવશ્યક પગલું છે, જેનો હેતુ પ્રોસેસ્ડ વેફર્સને બહુવિધ વ્યક્તિગત ડાયસમાં વિભાજીત કરવાનો છે. આ ડાયસમાં સામાન્ય રીતે સંપૂર્ણ સર્કિટ કાર્યક્ષમતા હોય છે અને તે ઇલેક્ટ્રોનિક ઉપકરણોના ઉત્પાદનમાં ઉપયોગમાં લેવાતા મુખ્ય ઘટકો છે. જેમ જેમ ચિપ ડિઝાઇન વધુ જટિલ બનતી જાય છે અને પરિમાણો સંકોચાતા રહે છે, તેમ તેમ વેફર ડાયસિંગ ટેકનોલોજી માટે ચોકસાઇ અને કાર્યક્ષમતાની આવશ્યકતાઓ વધુને વધુ કડક બનતી જાય છે.
વ્યવહારુ કામગીરીમાં, વેફર ડાઇસિંગ સામાન્ય રીતે ડાયમંડ બ્લેડ જેવા ઉચ્ચ-ચોકસાઇવાળા સાધનોનો ઉપયોગ કરે છે જેથી ખાતરી થાય કે દરેક ડાઇ અકબંધ અને સંપૂર્ણ રીતે કાર્યરત રહે. મુખ્ય પગલાંઓમાં કાપતા પહેલા તૈયારી, કાપવાની પ્રક્રિયા દરમિયાન ચોક્કસ નિયંત્રણ અને કાપ્યા પછી ગુણવત્તા નિરીક્ષણનો સમાવેશ થાય છે.
કાપતા પહેલા, વેફરને ચિહ્નિત કરવું અને સ્થાન આપવું આવશ્યક છે જેથી ચોક્કસ કટીંગ પાથ સુનિશ્ચિત થાય. કાપતી વખતે, વેફરને નુકસાન અટકાવવા માટે ટૂલ પ્રેશર અને ગતિ જેવા પરિમાણોને સખત રીતે નિયંત્રિત કરવા આવશ્યક છે. કાપ્યા પછી, દરેક ચિપ કામગીરીના ધોરણોને પૂર્ણ કરે છે તેની ખાતરી કરવા માટે વ્યાપક ગુણવત્તા નિરીક્ષણો હાથ ધરવામાં આવે છે.
વેફર ડાઇસિંગ ટેકનોલોજીના મૂળભૂત સિદ્ધાંતોમાં ફક્ત કટીંગ સાધનોની પસંદગી અને પ્રક્રિયા પરિમાણોની સેટિંગ જ નહીં, પરંતુ કટીંગ ગુણવત્તા પર સામગ્રીના યાંત્રિક ગુણધર્મો અને લાક્ષણિકતાઓનો પ્રભાવ પણ શામેલ છે. ઉદાહરણ તરીકે, લો-કે ડાયલેક્ટ્રિક સિલિકોન વેફર્સ, તેમના હલકી ગુણવત્તાવાળા યાંત્રિક ગુણધર્મોને કારણે, કટીંગ દરમિયાન તાણ સાંદ્રતા માટે ખૂબ જ સંવેદનશીલ હોય છે, જેના કારણે ચીપિંગ અને ક્રેકીંગ જેવી નિષ્ફળતાઓ થાય છે. લો-કે સામગ્રીની ઓછી કઠિનતા અને બરડપણું તેમને યાંત્રિક બળ અથવા થર્મલ તાણ હેઠળ માળખાકીય નુકસાન માટે વધુ સંવેદનશીલ બનાવે છે, ખાસ કરીને કટીંગ દરમિયાન. ટૂલ અને વેફર સપાટી વચ્ચેનો સંપર્ક, ઉચ્ચ તાપમાન સાથે, તાણ સાંદ્રતાને વધુ વધારી શકે છે.
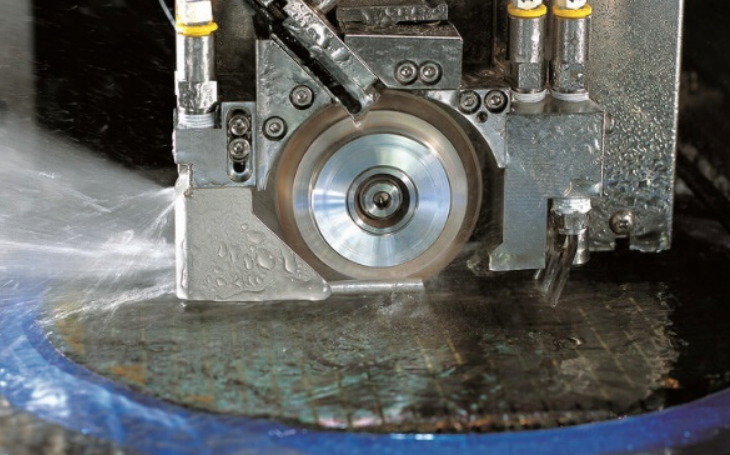
ભૌતિક વિજ્ઞાનમાં પ્રગતિ સાથે, વેફર ડાયસિંગ ટેકનોલોજી પરંપરાગત સિલિકોન-આધારિત સેમિકન્ડક્ટર્સથી આગળ વધીને ગેલિયમ નાઇટ્રાઇડ (GaN) જેવી નવી સામગ્રીનો સમાવેશ કરી રહી છે. આ નવી સામગ્રી, તેમની કઠિનતા અને માળખાકીય ગુણધર્મોને કારણે, ડાયસિંગ પ્રક્રિયાઓ માટે નવા પડકારો ઉભા કરે છે, જેના માટે કટીંગ ટૂલ્સ અને તકનીકોમાં વધુ સુધારાની જરૂર છે.
સેમિકન્ડક્ટર ઉદ્યોગમાં એક મહત્વપૂર્ણ પ્રક્રિયા તરીકે, વેફર ડાયસિંગને વિકસિત માંગ અને તકનીકી પ્રગતિના પ્રતિભાવમાં ઑપ્ટિમાઇઝ કરવાનું ચાલુ રાખવામાં આવ્યું છે, જે ભવિષ્યના માઇક્રોઇલેક્ટ્રોનિક્સ અને ઇન્ટિગ્રેટેડ સર્કિટ તકનીકો માટે પાયો નાખે છે.
વેફર ડાયસીંગ ટેકનોલોજીમાં સુધારાઓ સહાયક સામગ્રી અને સાધનોના વિકાસથી આગળ વધે છે. તેમાં પ્રક્રિયા ઑપ્ટિમાઇઝેશન, સાધનોના પ્રદર્શનમાં વધારો અને ડાયસીંગ પરિમાણોનું ચોક્કસ નિયંત્રણ પણ શામેલ છે. આ પ્રગતિઓનો ઉદ્દેશ વેફર ડાયસીંગ પ્રક્રિયામાં ઉચ્ચ ચોકસાઇ, કાર્યક્ષમતા અને સ્થિરતા સુનિશ્ચિત કરવાનો છે, જે સેમિકન્ડક્ટર ઉદ્યોગની નાના પરિમાણો, ઉચ્ચ એકીકરણ અને વધુ જટિલ ચિપ માળખાંની જરૂરિયાતને પૂર્ણ કરે છે.
સુધારણા ક્ષેત્ર | ચોક્કસ પગલાં | અસરો |
પ્રક્રિયા ઑપ્ટિમાઇઝેશન | - પ્રારંભિક તૈયારીઓમાં સુધારો કરો, જેમ કે વધુ સચોટ વેફર પોઝિશનિંગ અને પાથ પ્લાનિંગ. | - કટીંગ ભૂલો ઘટાડો અને સ્થિરતામાં સુધારો. |
- કટીંગ ભૂલો ઓછી કરો અને સ્થિરતા વધારો. | - ટૂલ પ્રેશર, સ્પીડ અને તાપમાનને સમાયોજિત કરવા માટે રીઅલ-ટાઇમ મોનિટરિંગ અને ફીડબેક મિકેનિઝમ્સ અપનાવો. | |
- વેફર તૂટવાનો દર ઓછો કરો અને ચિપ ગુણવત્તામાં સુધારો કરો. | ||
સાધનોની કામગીરીમાં વધારો | - ઉચ્ચ-ચોકસાઇવાળી યાંત્રિક પ્રણાલીઓ અને અદ્યતન ઓટોમેશન નિયંત્રણ ટેકનોલોજીનો ઉપયોગ કરો. | - કટીંગ ચોકસાઈ વધારવી અને સામગ્રીનો બગાડ ઘટાડવો. |
- ઉચ્ચ-કઠિનતાવાળા મટિરિયલ વેફર્સ માટે યોગ્ય લેસર કટીંગ ટેકનોલોજીનો પરિચય આપો. | - ઉત્પાદન કાર્યક્ષમતામાં સુધારો કરો અને મેન્યુઅલ ભૂલો ઘટાડો. | |
- ઓટોમેટિક મોનિટરિંગ અને ગોઠવણો માટે સાધનોના ઓટોમેશનમાં વધારો. | ||
ચોક્કસ પરિમાણ નિયંત્રણ | - કટીંગ ડેપ્થ, સ્પીડ, ટૂલ પ્રકાર અને કૂલિંગ પદ્ધતિઓ જેવા પરિમાણોને બારીકાઈથી ગોઠવો. | - ડાઇ ઇન્ટિગ્રિટી અને ઇલેક્ટ્રિકલ કામગીરીની ખાતરી કરો. |
- વેફર સામગ્રી, જાડાઈ અને બંધારણના આધારે પરિમાણોને કસ્ટમાઇઝ કરો. | - ઉપજ દરમાં વધારો, સામગ્રીનો બગાડ ઘટાડવો અને ઉત્પાદન ખર્ચ ઓછો કરવો. | |
વ્યૂહાત્મક મહત્વ | - બજારની માંગને પહોંચી વળવા માટે સતત નવા ટેકનોલોજીકલ માર્ગોનું અન્વેષણ કરો, પ્રક્રિયાઓને ઑપ્ટિમાઇઝ કરો અને સાધનોની ક્ષમતાઓમાં વધારો કરો. | - નવી સામગ્રી અને અદ્યતન ચિપ ડિઝાઇનના વિકાસને ટેકો આપીને, ચિપ ઉત્પાદન ઉપજ અને કામગીરીમાં સુધારો. |
૧.૨ વેફર ડાઇસિંગનું મહત્વ
સેમિકન્ડક્ટર ઉત્પાદન પ્રક્રિયામાં વેફર ડાયસિંગ મહત્વપૂર્ણ ભૂમિકા ભજવે છે, જે પછીના પગલાં તેમજ અંતિમ ઉત્પાદનની ગુણવત્તા અને પ્રદર્શન પર સીધી અસર કરે છે. તેનું મહત્વ નીચે મુજબ વિગતવાર વર્ણવી શકાય છે:
પ્રથમ, ડાયસિંગની ચોકસાઈ અને સુસંગતતા ચિપ ઉપજ અને વિશ્વસનીયતા સુનિશ્ચિત કરવા માટે ચાવીરૂપ છે. ઉત્પાદન દરમિયાન, વેફર્સ અનેક જટિલ સર્કિટ માળખાં બનાવવા માટે બહુવિધ પ્રક્રિયા પગલાંઓમાંથી પસાર થાય છે, જેને ચોક્કસ રીતે વ્યક્તિગત ચિપ્સ (ડાઇઝ) માં વિભાજિત કરવી આવશ્યક છે. જો ડાયસિંગ પ્રક્રિયા દરમિયાન ગોઠવણી અથવા કટીંગમાં નોંધપાત્ર ભૂલો હોય, તો સર્કિટને નુકસાન થઈ શકે છે, જે ચિપની કાર્યક્ષમતા અને વિશ્વસનીયતાને અસર કરે છે. તેથી, ઉચ્ચ-ચોકસાઇવાળા ડાયસિંગ ટેકનોલોજી માત્ર દરેક ચિપની અખંડિતતાને સુનિશ્ચિત કરતી નથી પરંતુ આંતરિક સર્કિટને નુકસાન અટકાવે છે, જેનાથી એકંદર ઉપજ દરમાં સુધારો થાય છે.
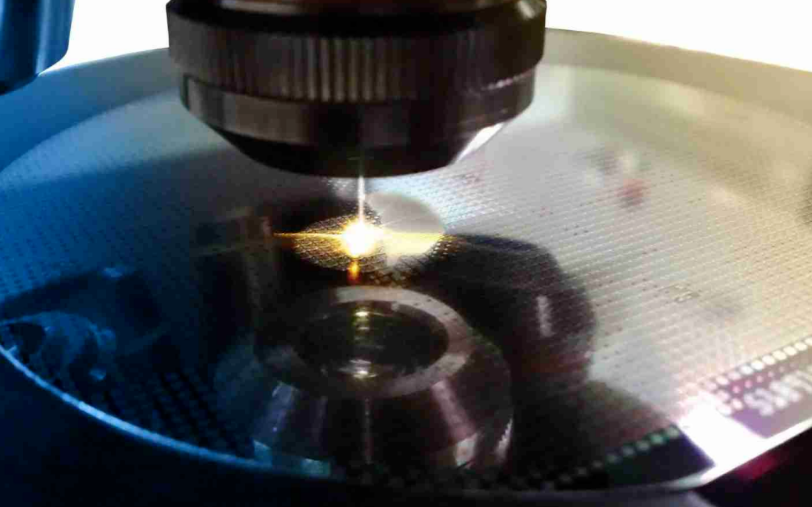
બીજું, વેફર ડાયસિંગ ઉત્પાદન કાર્યક્ષમતા અને ખર્ચ નિયંત્રણ પર નોંધપાત્ર અસર કરે છે. ઉત્પાદન પ્રક્રિયામાં એક મહત્વપૂર્ણ પગલું તરીકે, તેની કાર્યક્ષમતા અનુગામી પગલાંની પ્રગતિને સીધી અસર કરે છે. ડાયસિંગ પ્રક્રિયાને ઑપ્ટિમાઇઝ કરીને, ઓટોમેશન સ્તર વધારીને અને કટીંગ ઝડપમાં સુધારો કરીને, એકંદર ઉત્પાદન કાર્યક્ષમતામાં ઘણો વધારો કરી શકાય છે.
બીજી બાજુ, કાપણી દરમિયાન સામગ્રીનો બગાડ ખર્ચ વ્યવસ્થાપનમાં એક મહત્વપૂર્ણ પરિબળ છે. અદ્યતન કાપણી તકનીકોનો ઉપયોગ કરવાથી કાપણી પ્રક્રિયા દરમિયાન બિનજરૂરી સામગ્રીના નુકસાનમાં ઘટાડો થાય છે, પરંતુ વેફરનો ઉપયોગ પણ વધે છે, જેનાથી ઉત્પાદન ખર્ચ ઓછો થાય છે.
સેમિકન્ડક્ટર ટેકનોલોજીમાં પ્રગતિ સાથે, વેફર વ્યાસમાં વધારો થતો રહે છે, અને સર્કિટ ઘનતા તે મુજબ વધે છે, જેના કારણે ડાયસીંગ ટેકનોલોજી પર વધુ માંગણીઓ ઉભી થાય છે. મોટા વેફર્સને કટીંગ પાથના વધુ ચોક્કસ નિયંત્રણની જરૂર પડે છે, ખાસ કરીને ઉચ્ચ-ઘનતાવાળા સર્કિટ વિસ્તારોમાં, જ્યાં નાના વિચલનો પણ બહુવિધ ચિપ્સને ખામીયુક્ત બનાવી શકે છે. વધુમાં, મોટા વેફર્સમાં વધુ કટીંગ લાઇન અને વધુ જટિલ પ્રક્રિયા પગલાં શામેલ હોય છે, જેના કારણે આ પડકારોનો સામનો કરવા માટે ડાયસીંગ ટેકનોલોજીની ચોકસાઇ, સુસંગતતા અને કાર્યક્ષમતામાં વધુ સુધારાની જરૂર પડે છે.
૧.૩ વેફર ડાઇસિંગ પ્રક્રિયા
વેફર ડાઇસિંગ પ્રક્રિયામાં તૈયારીના તબક્કાથી લઈને અંતિમ ગુણવત્તા નિરીક્ષણ સુધીના તમામ પગલાંનો સમાવેશ થાય છે, જેમાં દરેક તબક્કો ડાઇસ કરેલી ચિપ્સની ગુણવત્તા અને કામગીરી સુનિશ્ચિત કરવા માટે મહત્વપૂર્ણ છે. નીચે દરેક તબક્કાની વિગતવાર સમજૂતી છે.
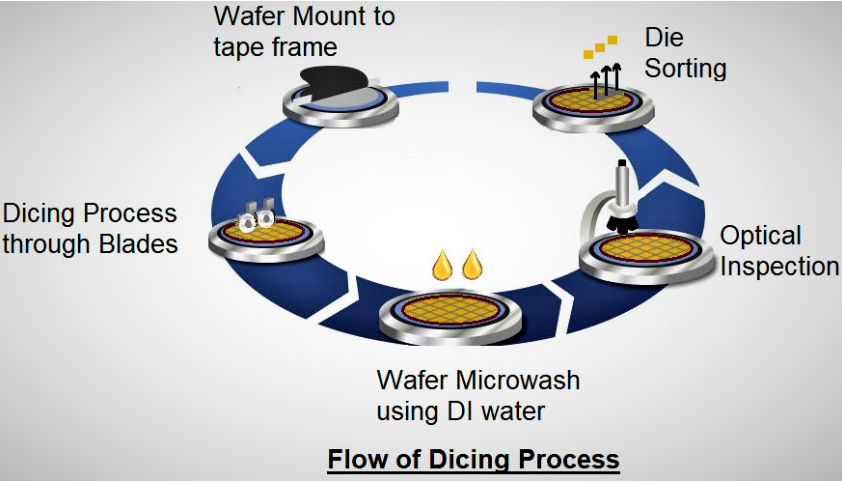
તબક્કો | વિગતવાર વર્ણન |
તૈયારીનો તબક્કો | -વેફર સફાઈ: સ્વચ્છ સપાટી સુનિશ્ચિત કરવા માટે, અશુદ્ધિઓ, કણો અને દૂષકોને દૂર કરવા માટે, ઉચ્ચ શુદ્ધતાવાળા પાણી અને વિશિષ્ટ સફાઈ એજન્ટોનો ઉપયોગ કરો, અલ્ટ્રાસોનિક અથવા યાંત્રિક સ્ક્રબિંગ સાથે. -ચોક્કસ સ્થિતિ: ડિઝાઇન કરેલા કટીંગ પાથ પર વેફરને સચોટ રીતે વિભાજીત કરવામાં આવે તેની ખાતરી કરવા માટે ઉચ્ચ-ચોકસાઇવાળા સાધનોનો ઉપયોગ કરો. -વેફર ફિક્સેશન: કટીંગ દરમિયાન સ્થિરતા જાળવવા માટે, કંપન અથવા હલનચલનથી નુકસાન અટકાવવા માટે વેફરને ટેપ ફ્રેમ પર સુરક્ષિત કરો. |
કટીંગ તબક્કો | -બ્લેડ ડાઇસિંગ: ભૌતિક કટીંગ માટે હાઇ-સ્પીડ ફરતા ડાયમંડ-કોટેડ બ્લેડનો ઉપયોગ કરો, જે સિલિકોન-આધારિત સામગ્રી માટે યોગ્ય અને ખર્ચ-અસરકારક છે. -લેસર ડાઇસિંગ: નોન-કોન્ટેક્ટ કટીંગ માટે ઉચ્ચ-ઊર્જા લેસર બીમનો ઉપયોગ કરો, જે ગેલિયમ નાઇટ્રાઇડ જેવી બરડ અથવા ઉચ્ચ-કઠિનતા સામગ્રી માટે આદર્શ છે, જે ઉચ્ચ ચોકસાઇ અને ઓછી સામગ્રી નુકશાન પ્રદાન કરે છે. -નવી ટેકનોલોજીઓ: ગરમીથી પ્રભાવિત ઝોનને ઘટાડીને કાર્યક્ષમતા અને ચોકસાઈમાં વધુ સુધારો કરવા માટે લેસર અને પ્લાઝ્મા કટીંગ ટેકનોલોજીનો પરિચય કરાવો. |
સફાઈ તબક્કો | - કાપતી વખતે ઉત્પન્ન થતા કાટમાળ અને ધૂળને દૂર કરવા માટે, ડીયોનાઇઝ્ડ વોટર (DI વોટર) અને વિશિષ્ટ સફાઈ એજન્ટોનો ઉપયોગ કરો, જે અલ્ટ્રાસોનિક અથવા સ્પ્રે સફાઈ સાથે જોડાયેલા હોય છે, જેથી અવશેષોને અનુગામી પ્રક્રિયાઓ અથવા ચિપ ઇલેક્ટ્રિકલ કામગીરીને અસર કરતા અટકાવી શકાય. - ઉચ્ચ શુદ્ધતા ધરાવતું DI પાણી નવા દૂષકોને દાખલ કરવાનું ટાળે છે, સ્વચ્છ વેફર વાતાવરણ સુનિશ્ચિત કરે છે. |
નિરીક્ષણ તબક્કો | -ઓપ્ટિકલ નિરીક્ષણ: ખામીઓને ઝડપથી ઓળખવા માટે, કાપેલી ચિપ્સમાં કોઈ તિરાડો કે ચીપિંગ ન થાય તેની ખાતરી કરવા, નિરીક્ષણ કાર્યક્ષમતામાં સુધારો કરવા અને માનવ ભૂલ ઘટાડવા માટે AI અલ્ગોરિધમ્સ સાથે જોડાયેલી ઓપ્ટિકલ ડિટેક્શન સિસ્ટમનો ઉપયોગ કરો. -પરિમાણ માપન: ચકાસો કે ચિપના પરિમાણો ડિઝાઇન સ્પષ્ટીકરણોને પૂર્ણ કરે છે. -ઇલેક્ટ્રિકલ પર્ફોર્મન્સ ટેસ્ટિંગ: ખાતરી કરો કે ક્રિટિકલ ચિપ્સનું વિદ્યુત પ્રદર્શન ધોરણોને પૂર્ણ કરે છે, જે પછીના ઉપયોગોમાં વિશ્વસનીયતાની ખાતરી આપે છે. |
સૉર્ટિંગ તબક્કો | - ટેપ ફ્રેમમાંથી લાયક ચિપ્સને અલગ કરવા માટે રોબોટિક આર્મ્સ અથવા વેક્યુમ સક્શન કપનો ઉપયોગ કરો અને કામગીરીના આધારે તેમને આપમેળે સૉર્ટ કરો, ઉત્પાદન કાર્યક્ષમતા અને સુગમતા સુનિશ્ચિત કરો અને ચોકસાઇમાં સુધારો કરો. |
વેફર કટીંગ પ્રક્રિયામાં વેફર ક્લિનિંગ, પોઝિશનિંગ, કટીંગ, ક્લિનિંગ, ઇન્સ્પેક્શન અને સોર્ટિંગનો સમાવેશ થાય છે, જેમાં દરેક પગલું મહત્વપૂર્ણ છે. ઓટોમેશન, લેસર કટીંગ અને એઆઈ ઇન્સ્પેક્શન ટેકનોલોજીમાં પ્રગતિ સાથે, આધુનિક વેફર કટીંગ સિસ્ટમ્સ ઉચ્ચ ચોકસાઇ, ગતિ અને ઓછી સામગ્રી નુકશાન પ્રાપ્ત કરી શકે છે. ભવિષ્યમાં, લેસર અને પ્લાઝ્મા જેવી નવી કટીંગ ટેકનોલોજીઓ ધીમે ધીમે પરંપરાગત બ્લેડ કટીંગને બદલે વધુને વધુ જટિલ ચિપ ડિઝાઇનની જરૂરિયાતોને પૂર્ણ કરશે, જે સેમિકન્ડક્ટર ઉત્પાદન પ્રક્રિયાઓના વિકાસને આગળ ધપાવશે.
વેફર કટીંગ ટેકનોલોજી અને તેના સિદ્ધાંતો
આ છબી ત્રણ સામાન્ય વેફર કટીંગ ટેકનોલોજી દર્શાવે છે:બ્લેડ ડાઇસિંગ,લેસર ડાઇસિંગ, અનેપ્લાઝ્મા ડાઇસિંગનીચે આ ત્રણ તકનીકોનું વિગતવાર વિશ્લેષણ અને પૂરક સમજૂતી છે:
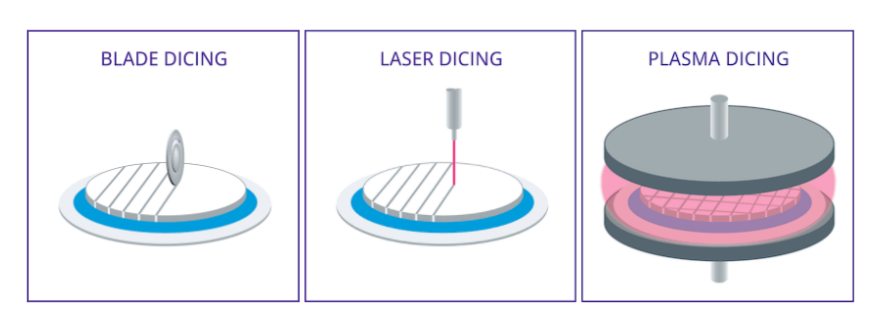
સેમિકન્ડક્ટર મેન્યુફેક્ચરિંગમાં, વેફર કટીંગ એ એક મહત્વપૂર્ણ પગલું છે જેમાં વેફરની જાડાઈના આધારે યોગ્ય કટીંગ પદ્ધતિ પસંદ કરવાની જરૂર પડે છે. પહેલું પગલું વેફરની જાડાઈ નક્કી કરવાનું છે. જો વેફરની જાડાઈ 100 માઇક્રોનથી વધુ હોય, તો બ્લેડ ડાયસીંગને કટીંગ પદ્ધતિ તરીકે પસંદ કરી શકાય છે. જો બ્લેડ ડાયસીંગ યોગ્ય ન હોય, તો ફ્રેક્ચર ડાયસીંગ પદ્ધતિનો ઉપયોગ કરી શકાય છે, જેમાં સ્ક્રિબ કટીંગ અને બ્લેડ ડાયસીંગ તકનીકો બંનેનો સમાવેશ થાય છે.
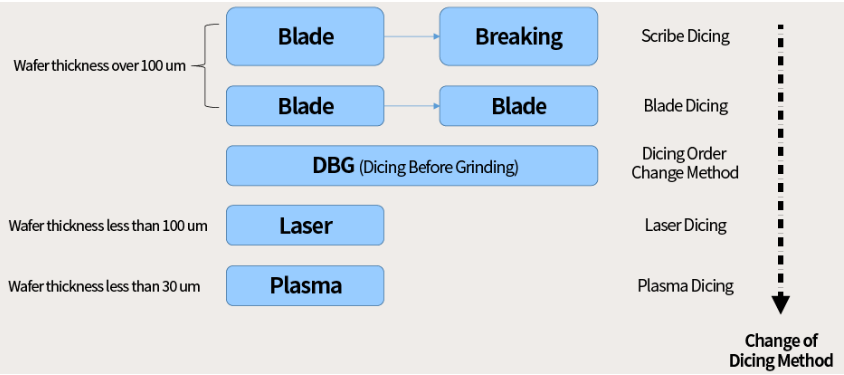
જ્યારે વેફરની જાડાઈ 30 થી 100 માઇક્રોન વચ્ચે હોય છે, ત્યારે DBG (ગ્રાઇન્ડીંગ પહેલાં ડાઇસ) પદ્ધતિની ભલામણ કરવામાં આવે છે. આ કિસ્સામાં, શ્રેષ્ઠ પરિણામો પ્રાપ્ત કરવા માટે સ્ક્રિબ કટીંગ, બ્લેડ ડાઇસીંગ અથવા જરૂર મુજબ કટીંગ ક્રમને સમાયોજિત કરવાનું પસંદ કરી શકાય છે.
30 માઇક્રોનથી ઓછી જાડાઈવાળા અતિ-પાતળા વેફર્સ માટે, લેસર કટીંગ વધુ પડતું નુકસાન પહોંચાડ્યા વિના પાતળા વેફર્સ કાપવાની ક્ષમતાને કારણે પસંદગીની પદ્ધતિ બની જાય છે. જો લેસર કટીંગ ચોક્કસ જરૂરિયાતોને પૂર્ણ કરી શકતું નથી, તો પ્લાઝ્મા કટીંગનો ઉપયોગ વિકલ્પ તરીકે કરી શકાય છે. આ ફ્લોચાર્ટ વિવિધ જાડાઈની પરિસ્થિતિઓમાં સૌથી યોગ્ય વેફર કટીંગ ટેકનોલોજી પસંદ કરવામાં આવે તેની ખાતરી કરવા માટે સ્પષ્ટ નિર્ણય લેવાનો માર્ગ પૂરો પાડે છે.
૨.૧ યાંત્રિક કટીંગ ટેકનોલોજી
વેફર ડાઇસિંગમાં યાંત્રિક કટીંગ ટેકનોલોજી પરંપરાગત પદ્ધતિ છે. મુખ્ય સિદ્ધાંત એ છે કે વેફરને કાપવા માટે હાઇ-સ્પીડ ફરતા ડાયમંડ ગ્રાઇન્ડીંગ વ્હીલનો ઉપયોગ કટીંગ ટૂલ તરીકે કરવો. મુખ્ય સાધનોમાં એર-બેરિંગ સ્પિન્ડલનો સમાવેશ થાય છે, જે ડાયમંડ ગ્રાઇન્ડીંગ વ્હીલ ટૂલને ઉચ્ચ ઝડપે ચલાવે છે જેથી પૂર્વનિર્ધારિત કટીંગ પાથ પર ચોક્કસ કટીંગ અથવા ગ્રુવિંગ કરી શકાય. આ ટેકનોલોજીનો ઉપયોગ તેની ઓછી કિંમત, ઉચ્ચ કાર્યક્ષમતા અને વ્યાપક ઉપયોગિતાને કારણે ઉદ્યોગમાં વ્યાપકપણે થાય છે.
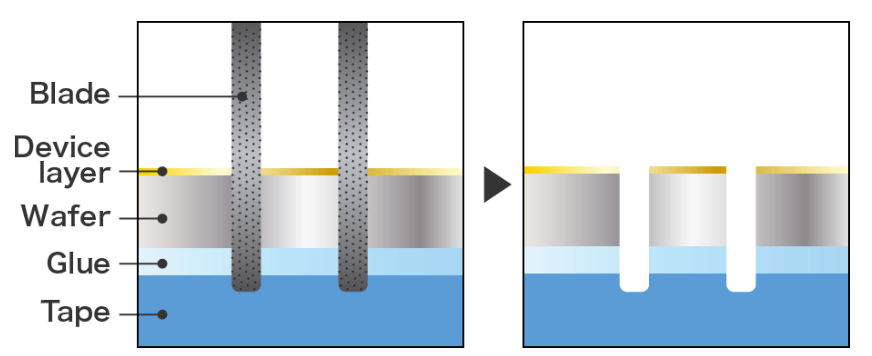
ફાયદા
ડાયમંડ ગ્રાઇન્ડીંગ વ્હીલ ટૂલ્સની ઉચ્ચ કઠિનતા અને ઘસારો પ્રતિકાર યાંત્રિક કટીંગ ટેકનોલોજીને વિવિધ વેફર સામગ્રીની કટીંગ જરૂરિયાતોને અનુરૂપ બનાવવા સક્ષમ બનાવે છે, પછી ભલે તે પરંપરાગત સિલિકોન-આધારિત સામગ્રી હોય કે નવા કમ્પાઉન્ડ સેમિકન્ડક્ટર. તેનું સંચાલન સરળ છે, પ્રમાણમાં ઓછી તકનીકી આવશ્યકતાઓ સાથે, મોટા પાયે ઉત્પાદનમાં તેની લોકપ્રિયતાને વધુ પ્રોત્સાહન આપે છે. વધુમાં, લેસર કટીંગ જેવી અન્ય કટીંગ પદ્ધતિઓની તુલનામાં, યાંત્રિક કટીંગનો ખર્ચ વધુ નિયંત્રિત થાય છે, જે તેને ઉચ્ચ-વોલ્યુમ ઉત્પાદન જરૂરિયાતો માટે યોગ્ય બનાવે છે.
મર્યાદાઓ
તેના અસંખ્ય ફાયદાઓ હોવા છતાં, યાંત્રિક કટીંગ ટેકનોલોજીની પણ મર્યાદાઓ છે. પ્રથમ, ટૂલ અને વેફર વચ્ચેના ભૌતિક સંપર્કને કારણે, કટીંગ ચોકસાઇ પ્રમાણમાં મર્યાદિત છે, જે ઘણીવાર પરિમાણીય વિચલનો તરફ દોરી જાય છે જે અનુગામી ચિપ પેકેજિંગ અને પરીક્ષણની ચોકસાઈને અસર કરી શકે છે. બીજું, યાંત્રિક કટીંગ પ્રક્રિયા દરમિયાન ચિપિંગ અને તિરાડો જેવી ખામીઓ સરળતાથી થઈ શકે છે, જે માત્ર ઉપજ દરને અસર કરતી નથી પરંતુ ચિપ્સની વિશ્વસનીયતા અને જીવનકાળને પણ નકારાત્મક અસર કરી શકે છે. યાંત્રિક તાણ-પ્રેરિત નુકસાન ખાસ કરીને ઉચ્ચ-ઘનતા ચિપ ઉત્પાદન માટે હાનિકારક છે, ખાસ કરીને જ્યારે બરડ સામગ્રી કાપતી વખતે, જ્યાં આ મુદ્દાઓ વધુ મુખ્ય હોય છે.
ટેકનોલોજીકલ સુધારાઓ
આ મર્યાદાઓને દૂર કરવા માટે, સંશોધકો યાંત્રિક કટીંગ પ્રક્રિયાને સતત ઑપ્ટિમાઇઝ કરી રહ્યા છે. મુખ્ય સુધારાઓમાં કટીંગ ચોકસાઇ અને ટકાઉપણું સુધારવા માટે ગ્રાઇન્ડીંગ વ્હીલ્સની ડિઝાઇન અને સામગ્રી પસંદગીમાં વધારો કરવાનો સમાવેશ થાય છે. વધુમાં, કટીંગ સાધનોની માળખાકીય ડિઝાઇન અને નિયંત્રણ પ્રણાલીઓને ઑપ્ટિમાઇઝ કરવાથી કટીંગ પ્રક્રિયાની સ્થિરતા અને ઓટોમેશનમાં વધુ સુધારો થયો છે. આ પ્રગતિઓ માનવ કામગીરીને કારણે થતી ભૂલોને ઘટાડે છે અને કટ્સની સુસંગતતામાં સુધારો કરે છે. કટીંગ પ્રક્રિયા દરમિયાન વિસંગતતાઓના વાસ્તવિક સમયના નિરીક્ષણ માટે અદ્યતન નિરીક્ષણ અને ગુણવત્તા નિયંત્રણ તકનીકોની રજૂઆતથી કટીંગ વિશ્વસનીયતા અને ઉપજમાં પણ નોંધપાત્ર સુધારો થયો છે.
ભવિષ્યનો વિકાસ અને નવી ટેકનોલોજીઓ
વેફર કટીંગમાં યાંત્રિક કટીંગ ટેકનોલોજી હજુ પણ મહત્વપૂર્ણ સ્થાન ધરાવે છે, તેમ છતાં સેમિકન્ડક્ટર પ્રક્રિયાઓ વિકસિત થતાં નવી કટીંગ ટેકનોલોજી ઝડપથી આગળ વધી રહી છે. ઉદાહરણ તરીકે, થર્મલ લેસર કટીંગ ટેકનોલોજીનો ઉપયોગ યાંત્રિક કટીંગમાં ચોકસાઇ અને ખામીના મુદ્દાઓ માટે નવા ઉકેલો પૂરા પાડે છે. આ બિન-સંપર્ક કટીંગ પદ્ધતિ વેફર પર ભૌતિક તાણ ઘટાડે છે, ખાસ કરીને વધુ બરડ સામગ્રી કાપતી વખતે ચીપિંગ અને ક્રેકીંગની ઘટનાઓને નોંધપાત્ર રીતે ઘટાડે છે. ભવિષ્યમાં, ઉભરતી કટીંગ તકનીકો સાથે યાંત્રિક કટીંગ ટેકનોલોજીનું એકીકરણ સેમિકન્ડક્ટર ઉત્પાદનને વધુ વિકલ્પો અને સુગમતા પ્રદાન કરશે, ઉત્પાદન કાર્યક્ષમતા અને ચિપ ગુણવત્તામાં વધુ વધારો કરશે.
નિષ્કર્ષમાં, યાંત્રિક કટીંગ ટેકનોલોજીમાં ચોક્કસ ખામીઓ હોવા છતાં, સતત તકનીકી સુધારાઓ અને નવી કટીંગ તકનીકો સાથે તેનું સંકલન તેને હજુ પણ સેમિકન્ડક્ટર ઉત્પાદનમાં મહત્વપૂર્ણ ભૂમિકા ભજવવા અને ભવિષ્યની પ્રક્રિયાઓમાં તેની સ્પર્ધાત્મકતા જાળવી રાખવા દે છે.
૨.૨ લેસર કટીંગ ટેકનોલોજી
વેફર કટીંગમાં નવી પદ્ધતિ તરીકે લેસર કટીંગ ટેકનોલોજી, તેની ઉચ્ચ ચોકસાઇ, યાંત્રિક સંપર્ક નુકસાનનો અભાવ અને ઝડપી કટીંગ ક્ષમતાઓને કારણે સેમિકન્ડક્ટર ઉદ્યોગમાં ધીમે ધીમે વ્યાપક ધ્યાન ખેંચી રહી છે. આ ટેકનોલોજી વેફર સામગ્રીની સપાટી પર એક નાનો ગરમી-અસરગ્રસ્ત ઝોન બનાવવા માટે લેસર બીમની ઉચ્ચ ઊર્જા ઘનતા અને ધ્યાન કેન્દ્રિત કરવાની ક્ષમતાનો ઉપયોગ કરે છે. જ્યારે લેસર બીમ વેફર પર લાગુ કરવામાં આવે છે, ત્યારે ઉત્પન્ન થર્મલ તણાવ સામગ્રીને નિર્ધારિત સ્થાન પર ફ્રેક્ચરનું કારણ બને છે, જેનાથી ચોક્કસ કટીંગ પ્રાપ્ત થાય છે.
લેસર કટીંગ ટેકનોલોજીના ફાયદા
• ઉચ્ચ ચોકસાઇ: લેસર બીમની ચોક્કસ સ્થિતિ ક્ષમતા માઇક્રોન અથવા તો નેનોમીટર-સ્તરની કટીંગ ચોકસાઇ માટે પરવાનગી આપે છે, જે આધુનિક ઉચ્ચ-ચોકસાઇ, ઉચ્ચ-ઘનતા સંકલિત સર્કિટ ઉત્પાદનની જરૂરિયાતોને પૂર્ણ કરે છે.
• કોઈ યાંત્રિક સંપર્ક નહીં: લેસર કટીંગ વેફર સાથે ભૌતિક સંપર્ક ટાળે છે, યાંત્રિક કટીંગમાં સામાન્ય સમસ્યાઓ, જેમ કે ચિપિંગ અને ક્રેકીંગને અટકાવે છે, જેનાથી ચિપ્સના ઉપજ દર અને વિશ્વસનીયતામાં નોંધપાત્ર સુધારો થાય છે.
• ઝડપી કટીંગ ગતિ: લેસર કટીંગની ઊંચી ઝડપ ઉત્પાદન કાર્યક્ષમતામાં વધારો કરે છે, જે તેને મોટા પાયે, ઊંચી ઝડપે ઉત્પાદન દૃશ્યો માટે ખાસ કરીને યોગ્ય બનાવે છે.
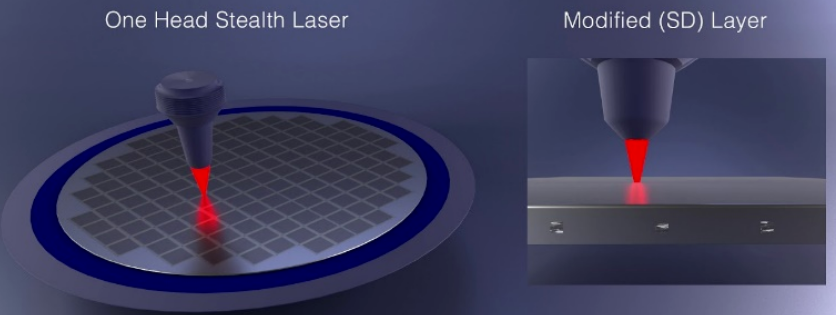
પડકારોનો સામનો કરવો પડ્યો
• ઉચ્ચ સાધનોનો ખર્ચ: લેસર કટીંગ સાધનો માટે પ્રારંભિક રોકાણ ઊંચું છે, જે આર્થિક દબાણ રજૂ કરે છે, ખાસ કરીને નાનાથી મધ્યમ કદના ઉત્પાદન સાહસો માટે.
• જટિલ પ્રક્રિયા નિયંત્રણ: લેસર કટીંગ માટે ઊર્જા ઘનતા, ફોકસ સ્થિતિ અને કટીંગ ઝડપ સહિત અનેક પરિમાણોનું ચોક્કસ નિયંત્રણ જરૂરી છે, જે પ્રક્રિયાને જટિલ બનાવે છે.
• ગરમીથી પ્રભાવિત ઝોન સમસ્યાઓ: લેસર કટીંગની સંપર્ક રહિત પ્રકૃતિ યાંત્રિક નુકસાન ઘટાડે છે, તેમ છતાં ગરમીથી પ્રભાવિત ઝોન (HAZ) ને કારણે થર્મલ તણાવ વેફર સામગ્રીના ગુણધર્મોને નકારાત્મક અસર કરી શકે છે. આ અસરને ઘટાડવા માટે પ્રક્રિયાના વધુ ઑપ્ટિમાઇઝેશનની જરૂર છે.
ટેકનોલોજીકલ સુધારણા દિશાઓ
આ પડકારોનો સામનો કરવા માટે, સંશોધકો સાધનોના ખર્ચ ઘટાડવા, કટીંગ કાર્યક્ષમતા સુધારવા અને પ્રક્રિયા પ્રવાહને ઑપ્ટિમાઇઝ કરવા પર ધ્યાન કેન્દ્રિત કરી રહ્યા છે.
• કાર્યક્ષમ લેસરો અને ઓપ્ટિકલ સિસ્ટમ્સ: વધુ કાર્યક્ષમ લેસરો અને અદ્યતન ઓપ્ટિકલ સિસ્ટમો વિકસાવીને, કટીંગ ચોકસાઇ અને ઝડપમાં વધારો કરતી વખતે સાધનોના ખર્ચમાં ઘટાડો શક્ય છે.
• પ્રક્રિયા પરિમાણોને ઑપ્ટિમાઇઝ કરવા: ગરમીથી પ્રભાવિત ઝોન ઘટાડતી પ્રક્રિયાઓને સુધારવા માટે લેસર અને વેફર સામગ્રી વચ્ચેની ક્રિયાપ્રતિક્રિયા પર ઊંડાણપૂર્વક સંશોધન હાથ ધરવામાં આવી રહ્યું છે, જેનાથી કટીંગ ગુણવત્તામાં સુધારો થાય છે.
• બુદ્ધિશાળી નિયંત્રણ સિસ્ટમો: બુદ્ધિશાળી નિયંત્રણ તકનીકોના વિકાસનો હેતુ લેસર કટીંગ પ્રક્રિયાને સ્વચાલિત અને ઑપ્ટિમાઇઝ કરવાનો છે, તેની સ્થિરતા અને સુસંગતતામાં સુધારો કરવાનો છે.
લેસર કટીંગ ટેકનોલોજી ખાસ કરીને અતિ-પાતળા વેફર્સ અને ઉચ્ચ-ચોકસાઇવાળા કટીંગ દૃશ્યોમાં અસરકારક છે. જેમ જેમ વેફરનું કદ વધે છે અને સર્કિટ ઘનતા વધે છે, તેમ તેમ પરંપરાગત યાંત્રિક કટીંગ પદ્ધતિઓ આધુનિક સેમિકન્ડક્ટર ઉત્પાદનની ઉચ્ચ-ચોકસાઇ અને ઉચ્ચ-કાર્યક્ષમતાની માંગને પૂર્ણ કરવામાં સંઘર્ષ કરે છે. તેના અનન્ય ફાયદાઓને કારણે, લેસર કટીંગ આ ક્ષેત્રોમાં પસંદગીનો ઉકેલ બની રહ્યું છે.
લેસર કટીંગ ટેકનોલોજી હજુ પણ ઉચ્ચ સાધનો ખર્ચ અને પ્રક્રિયા જટિલતા જેવા પડકારોનો સામનો કરે છે, તેમ છતાં ઉચ્ચ ચોકસાઇ અને બિન-સંપર્ક નુકસાનમાં તેના અનન્ય ફાયદાઓ તેને સેમિકન્ડક્ટર ઉત્પાદનમાં વિકાસ માટે એક મહત્વપૂર્ણ દિશા બનાવે છે. જેમ જેમ લેસર ટેકનોલોજી અને બુદ્ધિશાળી નિયંત્રણ પ્રણાલીઓ આગળ વધતી રહે છે, તેમ તેમ લેસર કટીંગ વેફર કટીંગ કાર્યક્ષમતા અને ગુણવત્તામાં વધુ સુધારો કરે તેવી અપેક્ષા છે, જે સેમિકન્ડક્ટર ઉદ્યોગના સતત વિકાસને આગળ ધપાવશે.
૨.૩ પ્લાઝ્મા કટીંગ ટેકનોલોજી
પ્લાઝ્મા કટીંગ ટેકનોલોજી, એક ઉભરતી વેફર ડાયસીંગ પદ્ધતિ તરીકે, તાજેતરના વર્ષોમાં નોંધપાત્ર ધ્યાન ખેંચી રહી છે. આ ટેકનોલોજી પ્લાઝ્મા બીમની ઊર્જા, ગતિ અને કટીંગ પાથને નિયંત્રિત કરીને વેફર્સને ચોક્કસ રીતે કાપવા માટે ઉચ્ચ-ઊર્જા પ્લાઝ્મા બીમનો ઉપયોગ કરે છે, જે શ્રેષ્ઠ કટીંગ પરિણામો પ્રાપ્ત કરે છે.
કાર્ય સિદ્ધાંત અને ફાયદા
પ્લાઝ્મા કટીંગની પ્રક્રિયા સાધનો દ્વારા ઉત્પન્ન થતા ઉચ્ચ-તાપમાન, ઉચ્ચ-ઊર્જા પ્લાઝ્મા બીમ પર આધાર રાખે છે. આ બીમ ખૂબ જ ઓછા સમયમાં વેફર સામગ્રીને તેના ગલન અથવા બાષ્પીભવન બિંદુ સુધી ગરમ કરી શકે છે, જેનાથી ઝડપી કટીંગ શક્ય બને છે. પરંપરાગત યાંત્રિક અથવા લેસર કટીંગની તુલનામાં, પ્લાઝ્મા કટીંગ ઝડપી છે અને એક નાનો ગરમી-અસરગ્રસ્ત ઝોન ઉત્પન્ન કરે છે, જે કટીંગ દરમિયાન તિરાડો અને નુકસાનની ઘટનાને અસરકારક રીતે ઘટાડે છે.
વ્યવહારુ એપ્લિકેશનોમાં, પ્લાઝ્મા કટીંગ ટેકનોલોજી ખાસ કરીને જટિલ આકારવાળા વેફર્સને હેન્ડલ કરવામાં પારંગત છે. તેનો ઉચ્ચ-ઊર્જા, એડજસ્ટેબલ પ્લાઝ્મા બીમ ઉચ્ચ ચોકસાઇ સાથે અનિયમિત આકારના વેફરને સરળતાથી કાપી શકે છે. તેથી, માઇક્રોઇલેક્ટ્રોનિક્સ ઉત્પાદનમાં, ખાસ કરીને ઉચ્ચ-અંતિમ ચિપ્સના કસ્ટમાઇઝ્ડ અને નાના-બેચ ઉત્પાદનમાં, આ ટેકનોલોજી વ્યાપક ઉપયોગ માટે મહાન આશાસ્પદ દર્શાવે છે.
પડકારો અને મર્યાદાઓ
પ્લાઝ્મા કટીંગ ટેકનોલોજીના ઘણા ફાયદા હોવા છતાં, તે કેટલાક પડકારોનો પણ સામનો કરે છે.
• જટિલ પ્રક્રિયા: પ્લાઝ્મા કટીંગ પ્રક્રિયા જટિલ છે અને તેને સુનિશ્ચિત કરવા માટે ઉચ્ચ-ચોકસાઇવાળા ઉપકરણો અને અનુભવી ઓપરેટરોની જરૂર પડે છેકટીંગમાં ચોકસાઈ અને સ્થિરતા.
• પર્યાવરણીય નિયંત્રણ અને સલામતી: પ્લાઝ્મા બીમના ઉચ્ચ-તાપમાન, ઉચ્ચ-ઊર્જા સ્વભાવને કારણે કડક પર્યાવરણીય નિયંત્રણ અને સલામતીના પગલાંની જરૂર પડે છે, જે અમલીકરણની જટિલતા અને ખર્ચમાં વધારો કરે છે.
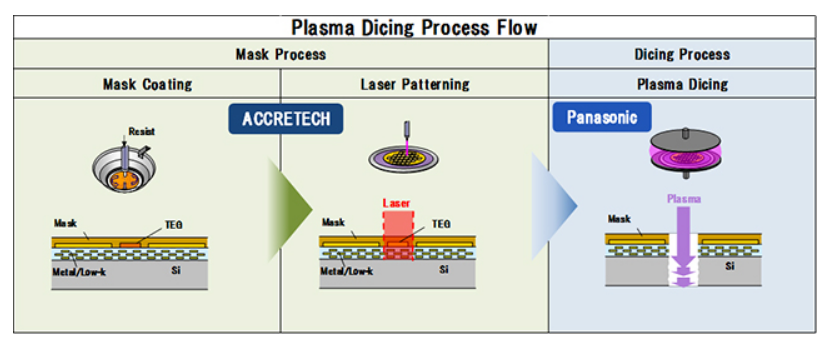
ભવિષ્યના વિકાસ દિશાઓ
ટેકનોલોજીકલ પ્રગતિ સાથે, પ્લાઝ્મા કટીંગ સાથે સંકળાયેલા પડકારો ધીમે ધીમે દૂર થવાની અપેક્ષા છે. વધુ સ્માર્ટ અને વધુ સ્થિર કટીંગ સાધનો વિકસાવીને, મેન્યુઅલ કામગીરી પરની નિર્ભરતા ઘટાડી શકાય છે, જેનાથી ઉત્પાદન કાર્યક્ષમતામાં સુધારો થાય છે. તે જ સમયે, પ્રક્રિયા પરિમાણો અને કટીંગ વાતાવરણને ઑપ્ટિમાઇઝ કરવાથી સલામતી જોખમો અને સંચાલન ખર્ચ ઘટાડવામાં મદદ મળશે.
સેમિકન્ડક્ટર ઉદ્યોગમાં, વેફર કટીંગ અને ડાયસીંગ ટેકનોલોજીમાં નવીનતાઓ ઉદ્યોગના વિકાસને આગળ ધપાવવા માટે મહત્વપૂર્ણ છે. પ્લાઝ્મા કટીંગ ટેકનોલોજી, તેની ઉચ્ચ ચોકસાઇ, કાર્યક્ષમતા અને જટિલ વેફર આકારોને હેન્ડલ કરવાની ક્ષમતા સાથે, આ ક્ષેત્રમાં એક મહત્વપૂર્ણ નવા ખેલાડી તરીકે ઉભરી આવી છે. જોકે કેટલાક પડકારો બાકી છે, આ મુદ્દાઓને ધીમે ધીમે સતત તકનીકી નવીનતા સાથે સંબોધવામાં આવશે, જે સેમિકન્ડક્ટર ઉત્પાદનમાં વધુ શક્યતાઓ અને તકો લાવશે.
પ્લાઝ્મા કટીંગ ટેકનોલોજીના ઉપયોગની સંભાવનાઓ વિશાળ છે, અને ભવિષ્યમાં તે સેમિકન્ડક્ટર ઉત્પાદનમાં વધુ મહત્વપૂર્ણ ભૂમિકા ભજવે તેવી અપેક્ષા છે. સતત તકનીકી નવીનતા અને ઑપ્ટિમાઇઝેશન દ્વારા, પ્લાઝ્મા કટીંગ માત્ર હાલના પડકારોનો સામનો કરશે નહીં પરંતુ સેમિકન્ડક્ટર ઉદ્યોગના વિકાસનું એક શક્તિશાળી ચાલક પણ બનશે.
૨.૪ ગુણવત્તામાં ઘટાડો અને પ્રભાવિત કરનારા પરિબળો
વેફર કટીંગ ગુણવત્તા અનુગામી ચિપ પેકેજિંગ, પરીક્ષણ અને અંતિમ ઉત્પાદનના એકંદર પ્રદર્શન અને વિશ્વસનીયતા માટે મહત્વપૂર્ણ છે. કટીંગ દરમિયાન આવતી સામાન્ય સમસ્યાઓમાં તિરાડો, ચિપિંગ અને કટીંગ વિચલનોનો સમાવેશ થાય છે. આ સમસ્યાઓ એકસાથે કામ કરતા ઘણા પરિબળોથી પ્રભાવિત થાય છે.
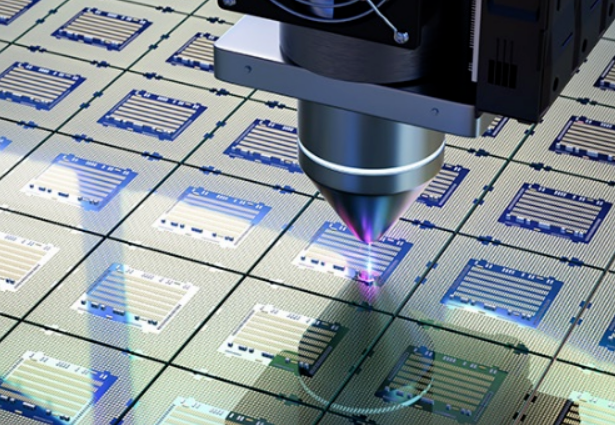
શ્રેણી | સામગ્રી | અસર |
પ્રક્રિયા પરિમાણો | કટીંગ સ્પીડ, ફીડ રેટ અને કટીંગ ડેપ્થ કટીંગ પ્રક્રિયાની સ્થિરતા અને ચોકસાઈ પર સીધી અસર કરે છે. અયોગ્ય સેટિંગ્સ તણાવ સાંદ્રતા અને વધુ પડતી ગરમી-અસરગ્રસ્ત ઝોન તરફ દોરી શકે છે, જેના પરિણામે તિરાડો અને ચીપ્સ થઈ શકે છે. વેફર સામગ્રી, જાડાઈ અને કટીંગ આવશ્યકતાઓના આધારે પરિમાણોને યોગ્ય રીતે ગોઠવવા એ ઇચ્છિત કટીંગ પરિણામો પ્રાપ્ત કરવાની ચાવી છે. | યોગ્ય પ્રક્રિયા પરિમાણો ચોક્કસ કટીંગ સુનિશ્ચિત કરે છે અને તિરાડો અને ચીપિંગ જેવી ખામીઓનું જોખમ ઘટાડે છે. |
સાધનો અને સામગ્રી પરિબળો | -બ્લેડ ગુણવત્તા: બ્લેડની સામગ્રી, કઠિનતા અને ઘસારો પ્રતિકાર કટીંગ પ્રક્રિયાની સરળતા અને કાપેલી સપાટીની સપાટતાને પ્રભાવિત કરે છે. નબળી-ગુણવત્તાવાળા બ્લેડ ઘર્ષણ અને થર્મલ તણાવમાં વધારો કરે છે, જે સંભવિત રીતે તિરાડો અથવા ચીપિંગ તરફ દોરી જાય છે. યોગ્ય બ્લેડ સામગ્રી પસંદ કરવી મહત્વપૂર્ણ છે. -શીતક કામગીરી: શીતક કટીંગ તાપમાન ઘટાડવામાં, ઘર્ષણ ઘટાડવામાં અને કાટમાળ સાફ કરવામાં મદદ કરે છે. બિનઅસરકારક શીતક ઊંચા તાપમાન અને કાટમાળ જમા થવા તરફ દોરી શકે છે, જે કટીંગ ગુણવત્તા અને કાર્યક્ષમતાને અસર કરે છે. કાર્યક્ષમ અને પર્યાવરણને અનુકૂળ શીતક પસંદ કરવા ખૂબ જ મહત્વપૂર્ણ છે. | બ્લેડની ગુણવત્તા કટની ચોકસાઈ અને સરળતાને અસર કરે છે. બિનઅસરકારક શીતક નબળી કટીંગ ગુણવત્તા અને કાર્યક્ષમતામાં પરિણમી શકે છે, જે શ્રેષ્ઠ શીતકના ઉપયોગની જરૂરિયાત પર ભાર મૂકે છે. |
પ્રક્રિયા નિયંત્રણ અને ગુણવત્તા નિરીક્ષણ | -પ્રક્રિયા નિયંત્રણ: કટીંગ પ્રક્રિયામાં સ્થિરતા અને સુસંગતતા સુનિશ્ચિત કરવા માટે મુખ્ય કટીંગ પરિમાણોનું રીઅલ-ટાઇમ મોનિટરિંગ અને ગોઠવણ. -ગુણવત્તા નિરીક્ષણ: કાપ્યા પછી દેખાવ તપાસ, પરિમાણીય માપન અને વિદ્યુત પ્રદર્શન પરીક્ષણ ગુણવત્તા સમસ્યાઓને તાત્કાલિક ઓળખવામાં અને તેનું નિરાકરણ કરવામાં મદદ કરે છે, કટીંગ ચોકસાઈ અને સુસંગતતામાં સુધારો કરે છે. | યોગ્ય પ્રક્રિયા નિયંત્રણ અને ગુણવત્તા નિરીક્ષણ સુસંગત, ઉચ્ચ-ગુણવત્તાવાળા કટીંગ પરિણામો અને સંભવિત સમસ્યાઓની વહેલી શોધ સુનિશ્ચિત કરવામાં મદદ કરે છે. |

કટીંગ ગુણવત્તામાં સુધારો
કટીંગ ગુણવત્તા સુધારવા માટે એક વ્યાપક અભિગમની જરૂર છે જેમાં પ્રક્રિયા પરિમાણો, સાધનો અને સામગ્રીની પસંદગી, પ્રક્રિયા નિયંત્રણ અને નિરીક્ષણનો સમાવેશ થાય છે. કટીંગ ટેકનોલોજીને સતત સુધારીને અને પ્રક્રિયા પદ્ધતિઓને ઑપ્ટિમાઇઝ કરીને, વેફર કટીંગની ચોકસાઈ અને સ્થિરતા વધુ વધારી શકાય છે, જે સેમિકન્ડક્ટર ઉત્પાદન ઉદ્યોગ માટે વધુ વિશ્વસનીય તકનીકી સહાય પૂરી પાડે છે.
#03 કટીંગ પછીનું સંચાલન અને પરીક્ષણ
૩.૧ સફાઈ અને સૂકવણી
વેફર કટીંગ પછી સફાઈ અને સૂકવણીના પગલાં ચિપની ગુણવત્તા અને અનુગામી પ્રક્રિયાઓની સરળ પ્રગતિ સુનિશ્ચિત કરવા માટે મહત્વપૂર્ણ છે. આ તબક્કા દરમિયાન, કટીંગ દરમિયાન ઉત્પન્ન થતા સિલિકોન કાટમાળ, શીતક અવશેષો અને અન્ય દૂષકોને સંપૂર્ણપણે દૂર કરવા જરૂરી છે. સફાઈ પ્રક્રિયા દરમિયાન ચિપ્સને નુકસાન ન થાય તેની ખાતરી કરવી પણ એટલી જ મહત્વપૂર્ણ છે, અને સૂકાયા પછી, કાટ અથવા ઇલેક્ટ્રોસ્ટેટિક ડિસ્ચાર્જ જેવી સમસ્યાઓને રોકવા માટે ચિપની સપાટી પર કોઈ ભેજ ન રહે તેની ખાતરી કરવી પણ એટલી જ મહત્વપૂર્ણ છે.
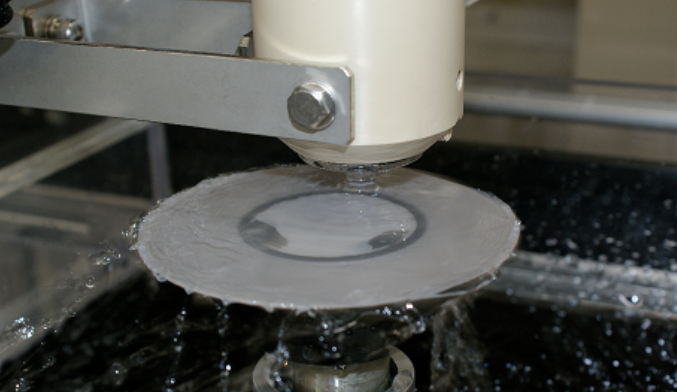
કાપ્યા પછીની સંભાળ: સફાઈ અને સૂકવણી પ્રક્રિયા
પ્રક્રિયા પગલું | સામગ્રી | અસર |
સફાઈ પ્રક્રિયા | -પદ્ધતિ: સફાઈ માટે વિશિષ્ટ સફાઈ એજન્ટો અને શુદ્ધ પાણીનો ઉપયોગ કરો, જેમાં અલ્ટ્રાસોનિક અથવા યાંત્રિક બ્રશિંગ તકનીકોનો સમાવેશ થાય છે. | દૂષકોને સંપૂર્ણ રીતે દૂર કરવાની ખાતરી આપે છે અને સફાઈ દરમિયાન ચિપ્સને થતા નુકસાનને અટકાવે છે. |
-સફાઈ એજન્ટની પસંદગી: ચિપને નુકસાન પહોંચાડ્યા વિના અસરકારક સફાઈ સુનિશ્ચિત કરવા માટે વેફર સામગ્રી અને દૂષક પ્રકાર પર આધારિત પસંદગી કરો. | અસરકારક સફાઈ અને ચિપ સુરક્ષા માટે યોગ્ય એજન્ટ પસંદગી ચાવીરૂપ છે. | |
-પરિમાણ નિયંત્રણ: અયોગ્ય સફાઈને કારણે ગુણવત્તાની સમસ્યાઓ અટકાવવા માટે સફાઈ તાપમાન, સમય અને સફાઈ દ્રાવણની સાંદ્રતાને સખત રીતે નિયંત્રિત કરો. | નિયંત્રણો વેફરને નુકસાન પહોંચાડવાનું અથવા દૂષકોને પાછળ છોડવાનું ટાળવામાં મદદ કરે છે, જેનાથી સુસંગત ગુણવત્તા સુનિશ્ચિત થાય છે. | |
સૂકવણી પ્રક્રિયા | -પરંપરાગત પદ્ધતિઓ: કુદરતી હવામાં સૂકવણી અને ગરમ હવામાં સૂકવણી, જેની કાર્યક્ષમતા ઓછી હોય છે અને તે સ્થિર વીજળીના સંચય તરફ દોરી શકે છે. | સૂકવણીનો સમય ધીમો પડી શકે છે અને સંભવિત સ્થિર સમસ્યાઓ થઈ શકે છે. |
-આધુનિક ટેકનોલોજીઓ: ચિપ્સ ઝડપથી સુકાઈ જાય અને હાનિકારક અસરો ટાળવા માટે વેક્યુમ ડ્રાયિંગ અને ઇન્ફ્રારેડ ડ્રાયિંગ જેવી અદ્યતન તકનીકોનો ઉપયોગ કરો. | ઝડપી અને વધુ કાર્યક્ષમ સૂકવણી પ્રક્રિયા, સ્થિર સ્રાવ અથવા ભેજ સંબંધિત સમસ્યાઓનું જોખમ ઘટાડે છે. | |
સાધનોની પસંદગી અને જાળવણી | -સાધનોની પસંદગી: ઉચ્ચ-પ્રદર્શન સફાઈ અને સૂકવણી મશીનો પ્રક્રિયા કાર્યક્ષમતામાં સુધારો કરે છે અને હેન્ડલિંગ દરમિયાન સંભવિત સમસ્યાઓને બારીકાઈથી નિયંત્રિત કરે છે. | ઉચ્ચ-ગુણવત્તાવાળા મશીનો વધુ સારી પ્રક્રિયા સુનિશ્ચિત કરે છે અને સફાઈ અને સૂકવણી દરમિયાન ભૂલોની સંભાવના ઘટાડે છે. |
-સાધનો જાળવણી: સાધનોનું નિયમિત નિરીક્ષણ અને જાળવણી ખાતરી કરે છે કે તે શ્રેષ્ઠ કાર્યકારી સ્થિતિમાં રહે છે, ચિપ ગુણવત્તાની ખાતરી આપે છે. | યોગ્ય જાળવણી સાધનોની નિષ્ફળતાને અટકાવે છે, વિશ્વસનીય અને ઉચ્ચ-ગુણવત્તાવાળી પ્રક્રિયા સુનિશ્ચિત કરે છે. |
કાપ્યા પછી સફાઈ અને સૂકવણી
વેફર કટીંગ પછી સફાઈ અને સૂકવણીના પગલાં જટિલ અને નાજુક પ્રક્રિયાઓ છે જેને અંતિમ પ્રક્રિયા પરિણામ સુનિશ્ચિત કરવા માટે બહુવિધ પરિબળોનો કાળજીપૂર્વક વિચાર કરવો જરૂરી છે. વૈજ્ઞાનિક પદ્ધતિઓ અને કઠોર પ્રક્રિયાઓનો ઉપયોગ કરીને, ખાતરી કરવી શક્ય છે કે દરેક ચિપ શ્રેષ્ઠ સ્થિતિમાં અનુગામી પેકેજિંગ અને પરીક્ષણ તબક્કામાં પ્રવેશ કરે છે.
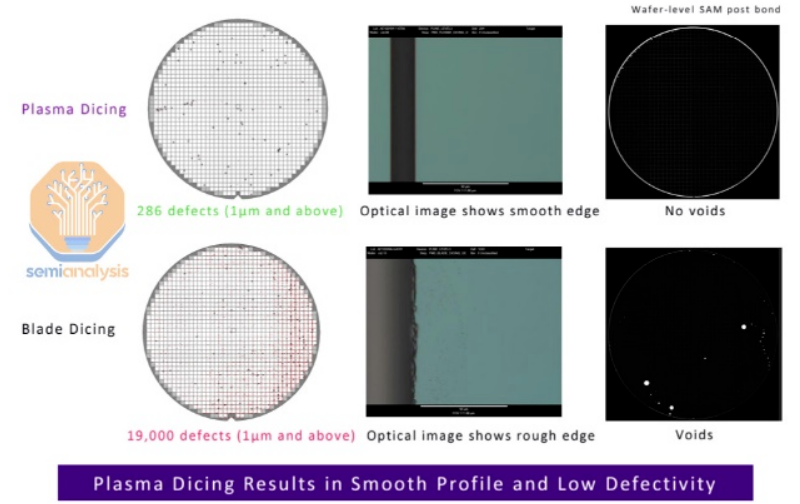
કાપણી પછીનું નિરીક્ષણ અને પરીક્ષણ
પગલું | સામગ્રી | અસર |
નિરીક્ષણ પગલું | ૧.દ્રશ્ય નિરીક્ષણ: ચિપની સપાટી પર તિરાડો, ચીપિંગ અથવા દૂષણ જેવી દૃશ્યમાન ખામીઓ તપાસવા માટે દ્રશ્ય અથવા સ્વચાલિત નિરીક્ષણ સાધનોનો ઉપયોગ કરો. બગાડ ટાળવા માટે ભૌતિક રીતે ક્ષતિગ્રસ્ત ચિપ્સને ઝડપથી ઓળખો. | પ્રક્રિયાની શરૂઆતમાં ખામીયુક્ત ચિપ્સને ઓળખવામાં અને દૂર કરવામાં મદદ કરે છે, જેનાથી સામગ્રીનું નુકસાન ઓછું થાય છે. |
2.કદ માપન: ચિપના પરિમાણોને સચોટ રીતે માપવા માટે ચોકસાઇ માપન ઉપકરણોનો ઉપયોગ કરો, ખાતરી કરો કે કટ કદ ડિઝાઇન સ્પષ્ટીકરણોને પૂર્ણ કરે છે અને કામગીરી સમસ્યાઓ અથવા પેકેજિંગ મુશ્કેલીઓને અટકાવે છે. | ખાતરી કરે છે કે ચિપ્સ જરૂરી કદ મર્યાદામાં છે, જે કામગીરીમાં ઘટાડો અથવા એસેમ્બલી સમસ્યાઓ અટકાવે છે. | |
૩.ઇલેક્ટ્રિકલ પર્ફોર્મન્સ ટેસ્ટિંગ: બિન-અનુપાલક ચિપ્સને ઓળખવા અને માત્ર પ્રદર્શન-લાયક ચિપ્સ જ આગળના તબક્કામાં આગળ વધે તેની ખાતરી કરવા માટે, પ્રતિકાર, કેપેસીટન્સ અને ઇન્ડક્ટન્સ જેવા મુખ્ય વિદ્યુત પરિમાણોનું મૂલ્યાંકન કરો. | પ્રક્રિયામાં ફક્ત કાર્યાત્મક અને પ્રદર્શન-પરીક્ષણ કરાયેલ ચિપ્સ જ આગળ વધે તેની ખાતરી કરે છે, જે પછીના તબક્કામાં નિષ્ફળતાનું જોખમ ઘટાડે છે. | |
પરીક્ષણ પગલું | ૧.કાર્યાત્મક પરીક્ષણ: ચકાસો કે ચિપની મૂળભૂત કાર્યક્ષમતા હેતુ મુજબ કાર્ય કરે છે, કાર્યાત્મક અસામાન્યતાઓ ધરાવતી ચિપ્સને ઓળખે છે અને દૂર કરે છે. | પછીના તબક્કામાં આગળ વધતા પહેલા ખાતરી કરે છે કે ચિપ્સ મૂળભૂત ઓપરેશનલ આવશ્યકતાઓને પૂર્ણ કરે છે. |
2.વિશ્વસનીયતા પરીક્ષણ: લાંબા સમય સુધી ઉપયોગ અથવા કઠોર વાતાવરણમાં ચિપ પ્રદર્શન સ્થિરતાનું મૂલ્યાંકન કરો, જેમાં સામાન્ય રીતે વાસ્તવિક દુનિયાની આત્યંતિક પરિસ્થિતિઓનું અનુકરણ કરવા માટે ઉચ્ચ-તાપમાન વૃદ્ધત્વ, નીચા-તાપમાન પરીક્ષણ અને ભેજ પરીક્ષણનો સમાવેશ થાય છે. | ખાતરી કરે છે કે ચિપ્સ વિવિધ પર્યાવરણીય પરિસ્થિતિઓમાં વિશ્વસનીય રીતે કાર્ય કરી શકે છે, ઉત્પાદનની આયુષ્ય અને સ્થિરતામાં સુધારો કરે છે. | |
૩.સુસંગતતા પરીક્ષણ: ખાતરી કરો કે ચિપ અન્ય ઘટકો અથવા સિસ્ટમો સાથે યોગ્ય રીતે કાર્ય કરે છે, ખાતરી કરો કે અસંગતતાને કારણે કોઈ ખામી અથવા પ્રદર્શનમાં ઘટાડો નથી. | સુસંગતતા સમસ્યાઓ અટકાવીને વાસ્તવિક દુનિયાની એપ્લિકેશનોમાં સરળ કામગીરી સુનિશ્ચિત કરે છે. |
૩.૩ પેકેજિંગ અને સંગ્રહ
વેફર કટીંગ પછી, ચિપ્સ સેમિકન્ડક્ટર ઉત્પાદન પ્રક્રિયાનો એક મહત્વપૂર્ણ આઉટપુટ છે, અને તેમના પેકેજિંગ અને સંગ્રહ તબક્કાઓ પણ એટલા જ મહત્વપૂર્ણ છે. યોગ્ય પેકેજિંગ અને સંગ્રહ પગલાં માત્ર પરિવહન અને સંગ્રહ દરમિયાન ચિપ્સની સલામતી અને સ્થિરતા સુનિશ્ચિત કરવા માટે જ નહીં પરંતુ અનુગામી ઉત્પાદન, પરીક્ષણ અને પેકેજિંગ તબક્કાઓ માટે મજબૂત સમર્થન પૂરું પાડવા માટે પણ જરૂરી છે.
નિરીક્ષણ અને પરીક્ષણ તબક્કાઓનો સારાંશ:
વેફર કટીંગ પછી ચિપ્સ માટે નિરીક્ષણ અને પરીક્ષણ પગલાં દ્રશ્ય નિરીક્ષણ, કદ માપન, વિદ્યુત પ્રદર્શન પરીક્ષણ, કાર્યાત્મક પરીક્ષણ, વિશ્વસનીયતા પરીક્ષણ અને સુસંગતતા પરીક્ષણ સહિત વિવિધ પાસાઓ આવરી લે છે. આ પગલાં એકબીજા સાથે જોડાયેલા અને પૂરક છે, જે ઉત્પાદનની ગુણવત્તા અને વિશ્વસનીયતા સુનિશ્ચિત કરવા માટે એક મજબૂત અવરોધ બનાવે છે. કડક નિરીક્ષણ અને પરીક્ષણ પ્રક્રિયાઓ દ્વારા, સંભવિત સમસ્યાઓ ઓળખી શકાય છે અને તાત્કાલિક ઉકેલી શકાય છે, ખાતરી કરીને કે અંતિમ ઉત્પાદન ગ્રાહકની જરૂરિયાતો અને અપેક્ષાઓને પૂર્ણ કરે છે.
પાસું | સામગ્રી |
પેકેજિંગ પગલાં | ૧.એન્ટિ-સ્ટેટિક: પેકેજિંગ સામગ્રીમાં ઉત્તમ એન્ટિ-સ્ટેટિક ગુણધર્મો હોવા જોઈએ જેથી સ્ટેટિક વીજળી ઉપકરણોને નુકસાન પહોંચાડતી નથી અથવા તેમના પ્રદર્શનને અસર કરતી નથી. |
2.ભેજ-પ્રતિરોધક: પેકેજિંગ સામગ્રીમાં ભેજ પ્રતિકારકતા સારી હોવી જોઈએ જેથી ભેજને કારણે કાટ લાગતો અટકાવી શકાય અને વિદ્યુત કામગીરીમાં બગાડ ન થાય. | |
૩.શોકપ્રૂફ: પેકેજિંગ સામગ્રીએ પરિવહન દરમિયાન ચિપ્સને કંપન અને અસરથી બચાવવા માટે અસરકારક આંચકા શોષણ પૂરું પાડવું જોઈએ. | |
સંગ્રહ વાતાવરણ | ૧.ભેજ નિયંત્રણ: વધુ પડતા ભેજને કારણે ભેજ શોષણ અને કાટ લાગવાથી બચવા માટે અથવા ઓછી ભેજને કારણે સ્થિર સમસ્યાઓથી બચવા માટે યોગ્ય શ્રેણીમાં ભેજને સખત રીતે નિયંત્રિત કરો. |
2.સ્વચ્છતા: ધૂળ અને અશુદ્ધિઓ દ્વારા ચિપ્સના દૂષણને ટાળવા માટે સ્વચ્છ સંગ્રહ વાતાવરણ જાળવો. | |
૩.તાપમાન નિયંત્રણ: વધુ પડતી ગરમી અથવા નીચા તાપમાનને કારણે ઘનીકરણની સમસ્યાઓને કારણે વૃદ્ધત્વને રોકવા માટે વાજબી તાપમાન શ્રેણી સેટ કરો અને તાપમાન સ્થિરતા જાળવી રાખો. | |
નિયમિત નિરીક્ષણ | સંગ્રહિત ચિપ્સનું નિયમિત નિરીક્ષણ અને મૂલ્યાંકન કરો, દ્રશ્ય નિરીક્ષણો, કદ માપન અને વિદ્યુત પ્રદર્શન પરીક્ષણોનો ઉપયોગ કરીને સમયસર સંભવિત સમસ્યાઓ ઓળખવા અને તેનું નિરાકરણ લાવવા માટે. સંગ્રહ સમય અને પરિસ્થિતિઓના આધારે, ચિપ્સનો ઉપયોગ શ્રેષ્ઠ સ્થિતિમાં થાય તેની ખાતરી કરવા માટે આયોજન કરો. |
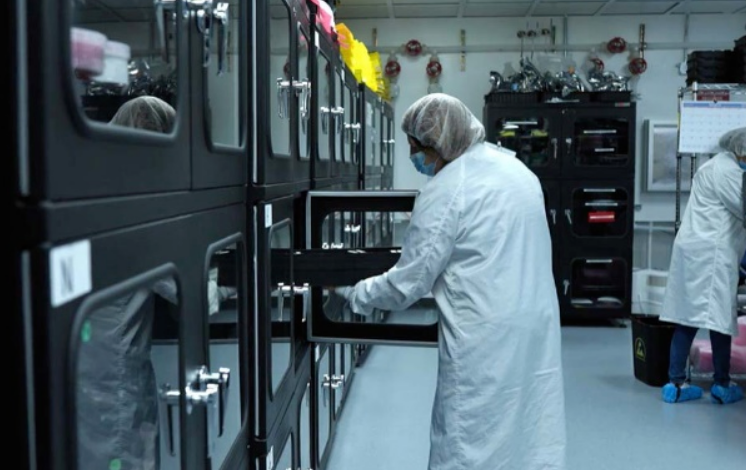
વેફર ડાયસીંગ પ્રક્રિયા દરમિયાન માઇક્રોક્રેક્સ અને નુકસાનનો મુદ્દો સેમિકન્ડક્ટર ઉત્પાદનમાં એક મહત્વપૂર્ણ પડકાર છે. કટીંગ સ્ટ્રેસ આ ઘટનાનું મુખ્ય કારણ છે, કારણ કે તે વેફર સપાટી પર નાની તિરાડો અને નુકસાન બનાવે છે, જેના કારણે ઉત્પાદન ખર્ચમાં વધારો થાય છે અને ઉત્પાદનની ગુણવત્તામાં ઘટાડો થાય છે.
આ પડકારનો સામનો કરવા માટે, કાપવાના તણાવને ઓછો કરવો અને ઑપ્ટિમાઇઝ્ડ કટીંગ તકનીકો, સાધનો અને પરિસ્થિતિઓનો અમલ કરવો ખૂબ જ મહત્વપૂર્ણ છે. બ્લેડ સામગ્રી, કાપવાની ગતિ, દબાણ અને ઠંડક પદ્ધતિઓ જેવા પરિબળો પર કાળજીપૂર્વક ધ્યાન આપવાથી માઇક્રોક્રેક્સનું નિર્માણ ઘટાડવામાં અને પ્રક્રિયાના એકંદર ઉપજમાં સુધારો કરવામાં મદદ મળી શકે છે. વધુમાં, લેસર ડાયસિંગ જેવી વધુ અદ્યતન કટીંગ તકનીકોમાં ચાલી રહેલા સંશોધન, આ સમસ્યાઓને વધુ ઘટાડવાના માર્ગો શોધી રહ્યા છે.
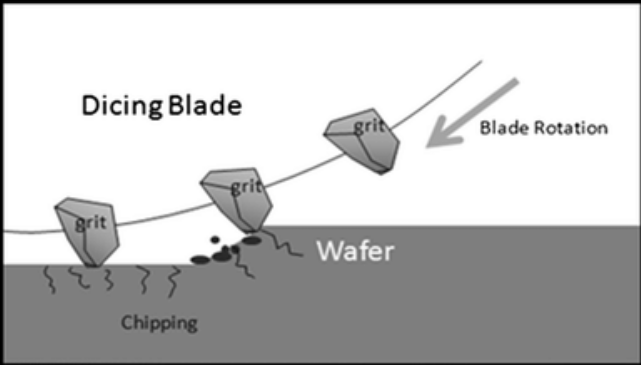
એક નાજુક સામગ્રી તરીકે, વેફર્સ યાંત્રિક, થર્મલ અથવા રાસાયણિક તાણને આધિન હોય ત્યારે આંતરિક માળખાકીય ફેરફારોનો ભોગ બને છે, જેના કારણે માઇક્રોક્રેક્સ બને છે. જોકે આ તિરાડો તાત્કાલિક ધ્યાનપાત્ર ન હોય શકે, તેમ છતાં ઉત્પાદન પ્રક્રિયા આગળ વધતાં તે વિસ્તૃત થઈ શકે છે અને વધુ ગંભીર નુકસાન પહોંચાડી શકે છે. આ સમસ્યા ખાસ કરીને અનુગામી પેકેજિંગ અને પરીક્ષણ તબક્કા દરમિયાન સમસ્યારૂપ બની જાય છે, જ્યાં તાપમાનમાં વધઘટ અને વધારાના યાંત્રિક તાણ આ માઇક્રોક્રેક્સને દૃશ્યમાન ફ્રેક્ચરમાં વિકસિત કરી શકે છે, જે સંભવિત રીતે ચિપ નિષ્ફળતા તરફ દોરી શકે છે.
આ જોખમ ઘટાડવા માટે, કટીંગ સ્પીડ, દબાણ અને તાપમાન જેવા પરિમાણોને ઑપ્ટિમાઇઝ કરીને કટીંગ પ્રક્રિયાને કાળજીપૂર્વક નિયંત્રિત કરવી જરૂરી છે. લેસર ડાયસીંગ જેવી ઓછી આક્રમક કટીંગ પદ્ધતિઓનો ઉપયોગ કરવાથી વેફર પરનો યાંત્રિક તાણ ઓછો થઈ શકે છે અને માઇક્રોક્રેક્સનું નિર્માણ ઓછું થઈ શકે છે. વધુમાં, વેફર ડાયસીંગ પ્રક્રિયા દરમિયાન ઇન્ફ્રારેડ સ્કેનિંગ અથવા એક્સ-રે ઇમેજિંગ જેવી અદ્યતન નિરીક્ષણ પદ્ધતિઓનો અમલ કરવાથી આ પ્રારંભિક તબક્કાની તિરાડો વધુ નુકસાન પહોંચાડે તે પહેલાં તેને શોધવામાં મદદ મળી શકે છે.
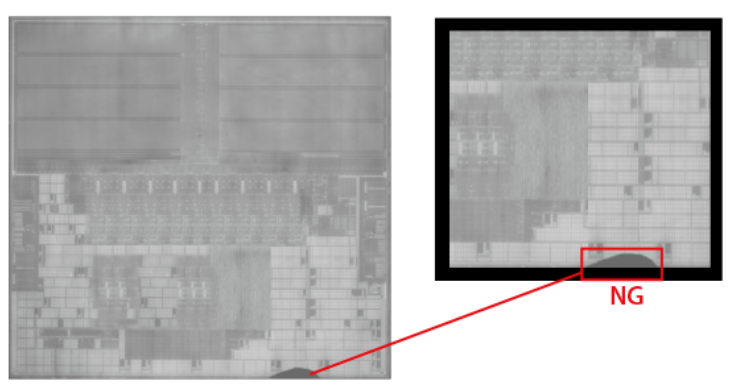
ડાઇસિંગ પ્રક્રિયામાં વેફર સપાટીને નુકસાન એ એક મહત્વપૂર્ણ ચિંતાનો વિષય છે, કારણ કે તે ચિપના પ્રદર્શન અને વિશ્વસનીયતા પર સીધી અસર કરી શકે છે. આવા નુકસાન કટીંગ ટૂલ્સના અયોગ્ય ઉપયોગ, ખોટા કટીંગ પરિમાણો અથવા વેફરમાં જ રહેલી સામગ્રી ખામીઓને કારણે થઈ શકે છે. કારણ ગમે તે હોય, આ નુકસાન સર્કિટના વિદ્યુત પ્રતિકાર અથવા કેપેસીટન્સમાં ફેરફાર તરફ દોરી શકે છે, જે એકંદર કામગીરીને અસર કરે છે.
આ મુદ્દાઓને ઉકેલવા માટે, બે મુખ્ય વ્યૂહરચનાઓ શોધવામાં આવી રહી છે:
1. કટીંગ ટૂલ્સ અને પરિમાણોને ઑપ્ટિમાઇઝ કરવું: તીક્ષ્ણ બ્લેડનો ઉપયોગ કરીને, કટીંગ ઝડપને સમાયોજિત કરીને અને કટીંગ ઊંડાઈમાં ફેરફાર કરીને, કટીંગ પ્રક્રિયા દરમિયાન તણાવની સાંદ્રતા ઘટાડી શકાય છે, આમ નુકસાનની સંભાવના ઘટાડે છે.
2. નવી કટીંગ ટેકનોલોજીઓનું અન્વેષણ: લેસર કટીંગ અને પ્લાઝ્મા કટીંગ જેવી અદ્યતન તકનીકો સુધારેલી ચોકસાઇ પ્રદાન કરે છે જ્યારે વેફર પર થતા નુકસાનનું સ્તર સંભવિત રીતે ઘટાડે છે. વેફર પર થર્મલ અને યાંત્રિક તાણ ઘટાડીને ઉચ્ચ કટીંગ ચોકસાઈ પ્રાપ્ત કરવાના રસ્તાઓ શોધવા માટે આ તકનીકોનો અભ્યાસ કરવામાં આવી રહ્યો છે.
થર્મલ ઇમ્પેક્ટ એરિયા અને કામગીરી પર તેની અસરો
લેસર અને પ્લાઝ્મા કટીંગ જેવી થર્મલ કટીંગ પ્રક્રિયાઓમાં, ઉચ્ચ તાપમાન અનિવાર્યપણે વેફરની સપાટી પર થર્મલ ઇમ્પેક્ટ ઝોન બનાવે છે. આ વિસ્તાર, જ્યાં તાપમાનનો ઢાળ નોંધપાત્ર છે, તે સામગ્રીના ગુણધર્મોને બદલી શકે છે, જે ચિપના અંતિમ પ્રદર્શનને અસર કરે છે.
થર્મલ અસરગ્રસ્ત ઝોન (TAZ) ની અસર:
સ્ફટિક માળખામાં ફેરફાર: ઊંચા તાપમાને, વેફર સામગ્રીની અંદરના અણુઓ ફરીથી ગોઠવાઈ શકે છે, જેના કારણે સ્ફટિક માળખામાં વિકૃતિઓ થાય છે. આ વિકૃતિ સામગ્રીને નબળી પાડે છે, તેની યાંત્રિક શક્તિ અને સ્થિરતા ઘટાડે છે, જે ઉપયોગ દરમિયાન ચિપ નિષ્ફળતાનું જોખમ વધારે છે.
વિદ્યુત ગુણધર્મોમાં ફેરફાર: ઉચ્ચ તાપમાન સેમિકન્ડક્ટર સામગ્રીમાં વાહક સાંદ્રતા અને ગતિશીલતાને બદલી શકે છે, જે ચિપની વિદ્યુત વાહકતા અને વર્તમાન ટ્રાન્સમિશન કાર્યક્ષમતાને અસર કરે છે. આ ફેરફારો ચિપની કામગીરીમાં ઘટાડો તરફ દોરી શકે છે, જે સંભવિત રીતે તેને તેના હેતુ માટે અયોગ્ય બનાવી શકે છે.
આ અસરોને ઘટાડવા માટે, કટીંગ દરમિયાન તાપમાનને નિયંત્રિત કરવું, કટીંગ પરિમાણોને ઑપ્ટિમાઇઝ કરવું, અને કૂલિંગ જેટ્સ અથવા પોસ્ટ-પ્રોસેસિંગ ટ્રીટમેન્ટ જેવી પદ્ધતિઓનું અન્વેષણ કરવું એ થર્મલ અસરની હદ ઘટાડવા અને સામગ્રીની અખંડિતતા જાળવવા માટે આવશ્યક વ્યૂહરચનાઓ છે.
એકંદરે, વેફર ડાઇસિંગ ટેકનોલોજીમાં માઇક્રોક્રેક્સ અને થર્મલ ઇમ્પેક્ટ ઝોન બંને મહત્વપૂર્ણ પડકારો છે. સેમિકન્ડક્ટર ઉત્પાદનોની ગુણવત્તા સુધારવા અને તેમની બજાર સ્પર્ધાત્મકતા વધારવા માટે ટેકનોલોજીકલ પ્રગતિ અને ગુણવત્તા નિયંત્રણ પગલાં સાથે સતત સંશોધન જરૂરી બનશે.
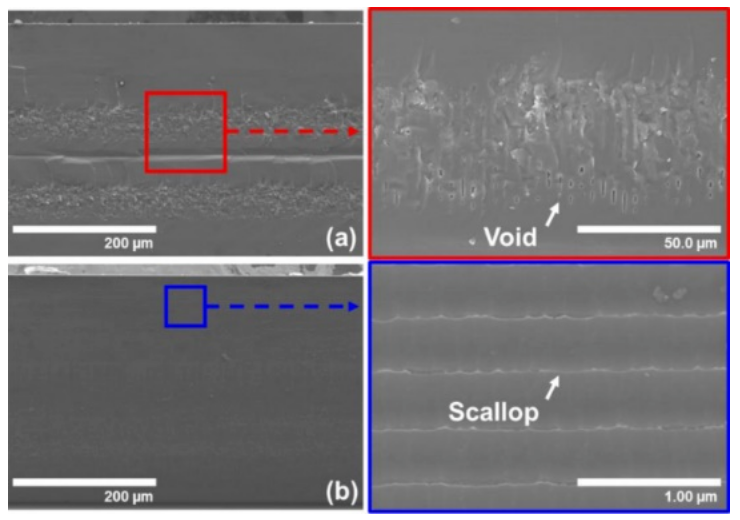
થર્મલ ઇમ્પેક્ટ ઝોનને નિયંત્રિત કરવાનાં પગલાં:
કટીંગ પ્રક્રિયા પરિમાણોને ઑપ્ટિમાઇઝ કરવું: કટીંગ સ્પીડ અને પાવર ઘટાડવાથી થર્મલ ઇમ્પેક્ટ ઝોન (TAZ) નું કદ અસરકારક રીતે ઘટાડી શકાય છે. આ કટીંગ પ્રક્રિયા દરમિયાન ઉત્પન્ન થતી ગરમીની માત્રાને નિયંત્રિત કરવામાં મદદ કરે છે, જે વેફરના મટીરીયલ ગુણધર્મોને સીધી અસર કરે છે.
એડવાન્સ્ડ કૂલિંગ ટેક્નોલોજીસ: લિક્વિડ નાઇટ્રોજન કૂલિંગ અને માઇક્રોફ્લુઇડિક કૂલિંગ જેવી ટેકનોલોજીનો ઉપયોગ થર્મલ ઇમ્પેક્ટ ઝોનની શ્રેણીને નોંધપાત્ર રીતે મર્યાદિત કરી શકે છે. આ ઠંડક પદ્ધતિઓ ગરમીને વધુ કાર્યક્ષમ રીતે દૂર કરવામાં મદદ કરે છે, આમ વેફરના ભૌતિક ગુણધર્મોને સાચવે છે અને થર્મલ નુકસાન ઘટાડે છે.
સામગ્રીની પસંદગી: સંશોધકો કાર્બન નેનોટ્યુબ અને ગ્રેફિન જેવા નવા પદાર્થોની શોધ કરી રહ્યા છે, જેમાં ઉત્તમ થર્મલ વાહકતા અને યાંત્રિક શક્તિ છે. આ સામગ્રી ચિપ્સના એકંદર પ્રદર્શનમાં સુધારો કરતી વખતે થર્મલ ઇમ્પેક્ટ ઝોન ઘટાડી શકે છે.
સારાંશમાં, થર્મલ ઇમ્પેક્ટ ઝોન થર્મલ કટીંગ ટેકનોલોજીનું અનિવાર્ય પરિણામ હોવા છતાં, તેને ઑપ્ટિમાઇઝ્ડ પ્રોસેસિંગ તકનીકો અને સામગ્રી પસંદગી દ્વારા અસરકારક રીતે નિયંત્રિત કરી શકાય છે. ભવિષ્યના સંશોધનમાં વધુ કાર્યક્ષમ અને ચોક્કસ વેફર ડાયસિંગ પ્રાપ્ત કરવા માટે થર્મલ કટીંગ પ્રક્રિયાઓને ફાઇન-ટ્યુનિંગ અને સ્વચાલિત કરવા પર ધ્યાન કેન્દ્રિત કરવામાં આવશે.

સંતુલન વ્યૂહરચના:
વેફર ડાયસીંગ ટેકનોલોજીમાં વેફર ઉપજ અને ઉત્પાદન કાર્યક્ષમતા વચ્ચે શ્રેષ્ઠ સંતુલન પ્રાપ્ત કરવું એ સતત પડકાર છે. ઉત્પાદકોએ તર્કસંગત ઉત્પાદન વ્યૂહરચના અને પ્રક્રિયા પરિમાણો વિકસાવવા માટે બજારની માંગ, ઉત્પાદન ખર્ચ અને ઉત્પાદન ગુણવત્તા જેવા અનેક પરિબળો ધ્યાનમાં લેવાની જરૂર છે. તે જ સમયે, ઉત્પાદન કાર્યક્ષમતામાં વધારો કરતી વખતે ઉપજ જાળવવા અથવા સુધારવા માટે અદ્યતન કટીંગ સાધનો રજૂ કરવા, ઓપરેટર કુશળતામાં સુધારો કરવો અને કાચા માલના ગુણવત્તા નિયંત્રણમાં વધારો કરવો જરૂરી છે.
ભવિષ્યના પડકારો અને તકો:
સેમિકન્ડક્ટર ટેકનોલોજીના વિકાસ સાથે, વેફર કટીંગ નવા પડકારો અને તકોનો સામનો કરે છે. જેમ જેમ ચિપનું કદ ઘટતું જાય છે અને એકીકરણ વધે છે, તેમ તેમ કટીંગ ચોકસાઈ અને ગુણવત્તાની માંગ નોંધપાત્ર રીતે વધે છે. તે જ સમયે, ઉભરતી તકનીકો વેફર કટીંગ તકનીકોના વિકાસ માટે નવા વિચારો પ્રદાન કરે છે. ઉત્પાદકોએ બજારની ગતિશીલતા અને તકનીકી વલણો સાથે સુસંગત રહેવું જોઈએ, બજારના ફેરફારો અને તકનીકી માંગણીઓને પહોંચી વળવા માટે ઉત્પાદન વ્યૂહરચનાઓ અને પ્રક્રિયા પરિમાણોને સતત સમાયોજિત અને ઑપ્ટિમાઇઝ કરવું જોઈએ.
નિષ્કર્ષમાં, બજારની માંગ, ઉત્પાદન ખર્ચ અને ઉત્પાદન ગુણવત્તાને ધ્યાનમાં લઈને, અને અદ્યતન સાધનો અને ટેકનોલોજી રજૂ કરીને, ઓપરેટર કૌશલ્યમાં વધારો કરીને અને કાચા માલના નિયંત્રણને મજબૂત બનાવીને, ઉત્પાદકો વેફર ડાયસિંગ દરમિયાન વેફર ઉપજ અને ઉત્પાદન કાર્યક્ષમતા વચ્ચે શ્રેષ્ઠ સંતુલન પ્રાપ્ત કરી શકે છે, જે કાર્યક્ષમ અને ઉચ્ચ-ગુણવત્તાવાળા સેમિકન્ડક્ટર ઉત્પાદન ઉત્પાદન તરફ દોરી જાય છે.
ભવિષ્યની સંભાવનાઓ:
ઝડપી ટેકનોલોજીકલ પ્રગતિ સાથે, સેમિકન્ડક્ટર ટેકનોલોજી અભૂતપૂર્વ ગતિએ આગળ વધી રહી છે. સેમિકન્ડક્ટર ઉત્પાદનમાં એક મહત્વપૂર્ણ પગલા તરીકે, વેફર કટીંગ ટેકનોલોજી નવા ઉત્તેજક વિકાસ માટે તૈયાર છે. આગળ જોતાં, વેફર કટીંગ ટેકનોલોજી ચોકસાઇ, કાર્યક્ષમતા અને ખર્ચમાં નોંધપાત્ર સુધારા પ્રાપ્ત કરશે તેવી અપેક્ષા છે, જે સેમિકન્ડક્ટર ઉદ્યોગના સતત વિકાસમાં નવી જોમ ઉમેરશે.
ચોકસાઇમાં વધારો:
ઉચ્ચ ચોકસાઇ મેળવવા માટે, વેફર કટીંગ ટેકનોલોજી સતત હાલની પ્રક્રિયાઓની મર્યાદાઓને આગળ ધપાવશે. કટીંગ પ્રક્રિયાના ભૌતિક અને રાસાયણિક મિકેનિઝમ્સનો ઊંડાણપૂર્વક અભ્યાસ કરીને અને કટીંગ પરિમાણોને ચોક્કસ રીતે નિયંત્રિત કરીને, વધુને વધુ જટિલ સર્કિટ ડિઝાઇન આવશ્યકતાઓને પૂર્ણ કરવા માટે ઝીણા કટીંગ પરિણામો પ્રાપ્ત કરવામાં આવશે. વધુમાં, નવી સામગ્રી અને કટીંગ પદ્ધતિઓનું સંશોધન ઉપજ અને ગુણવત્તામાં નોંધપાત્ર સુધારો કરશે.
કાર્યક્ષમતા વધારવી:
નવા વેફર કટીંગ સાધનો સ્માર્ટ અને ઓટોમેટેડ ડિઝાઇન પર ધ્યાન કેન્દ્રિત કરશે. અદ્યતન નિયંત્રણ પ્રણાલીઓ અને અલ્ગોરિધમ્સની રજૂઆતથી સાધનો વિવિધ સામગ્રી અને ડિઝાઇન આવશ્યકતાઓને સમાયોજિત કરવા માટે કટીંગ પરિમાણોને આપમેળે ગોઠવી શકશે, આમ ઉત્પાદન કાર્યક્ષમતામાં નોંધપાત્ર સુધારો થશે. મલ્ટી-વેફર કટીંગ ટેકનોલોજી અને ઝડપી બ્લેડ રિપ્લેસમેન્ટ સિસ્ટમ્સ જેવી નવીનતાઓ કાર્યક્ષમતા વધારવામાં મહત્વપૂર્ણ ભૂમિકા ભજવશે.
ખર્ચ ઘટાડવો:
વેફર કટીંગ ટેકનોલોજીના વિકાસ માટે ખર્ચ ઘટાડવો એ એક મુખ્ય દિશા છે. જેમ જેમ નવી સામગ્રી અને કટીંગ પદ્ધતિઓ વિકસાવવામાં આવે છે, તેમ તેમ સાધનોના ખર્ચ અને જાળવણી ખર્ચને અસરકારક રીતે નિયંત્રિત કરવાની અપેક્ષા છે. વધુમાં, ઉત્પાદન પ્રક્રિયાઓને ઑપ્ટિમાઇઝ કરવા અને સ્ક્રેપ દર ઘટાડવાથી ઉત્પાદન દરમિયાન કચરો વધુ ઘટશે, જેના કારણે એકંદર ઉત્પાદન ખર્ચમાં ઘટાડો થશે.
સ્માર્ટ મેન્યુફેક્ચરિંગ અને IoT:
સ્માર્ટ મેન્યુફેક્ચરિંગ અને ઇન્ટરનેટ ઓફ થિંગ્સ (IoT) ટેકનોલોજીનું એકીકરણ વેફર કટીંગ ટેકનોલોજીમાં પરિવર્તનશીલ ફેરફારો લાવશે. ઉપકરણો વચ્ચે ઇન્ટરકનેક્ટિવિટી અને ડેટા શેરિંગ દ્વારા, ઉત્પાદન પ્રક્રિયાના દરેક પગલાનું વાસ્તવિક સમયમાં નિરીક્ષણ અને ઑપ્ટિમાઇઝ કરી શકાય છે. આ માત્ર ઉત્પાદન કાર્યક્ષમતા અને ઉત્પાદન ગુણવત્તામાં સુધારો કરતું નથી પરંતુ કંપનીઓને વધુ સચોટ બજાર આગાહી અને નિર્ણય લેવામાં સહાય પણ પૂરી પાડે છે.
ભવિષ્યમાં, વેફર કટીંગ ટેકનોલોજી ચોકસાઇ, કાર્યક્ષમતા અને ખર્ચમાં નોંધપાત્ર પ્રગતિ કરશે. આ પ્રગતિઓ સેમિકન્ડક્ટર ઉદ્યોગના સતત વિકાસને આગળ ધપાવશે અને માનવ સમાજમાં વધુ તકનીકી નવીનતાઓ અને સુવિધાઓ લાવશે.
પોસ્ટ સમય: નવેમ્બર-૧૯-૨૦૨૪